CNC Machining Parts: A Comprehensive Guide for Metal Fabricators
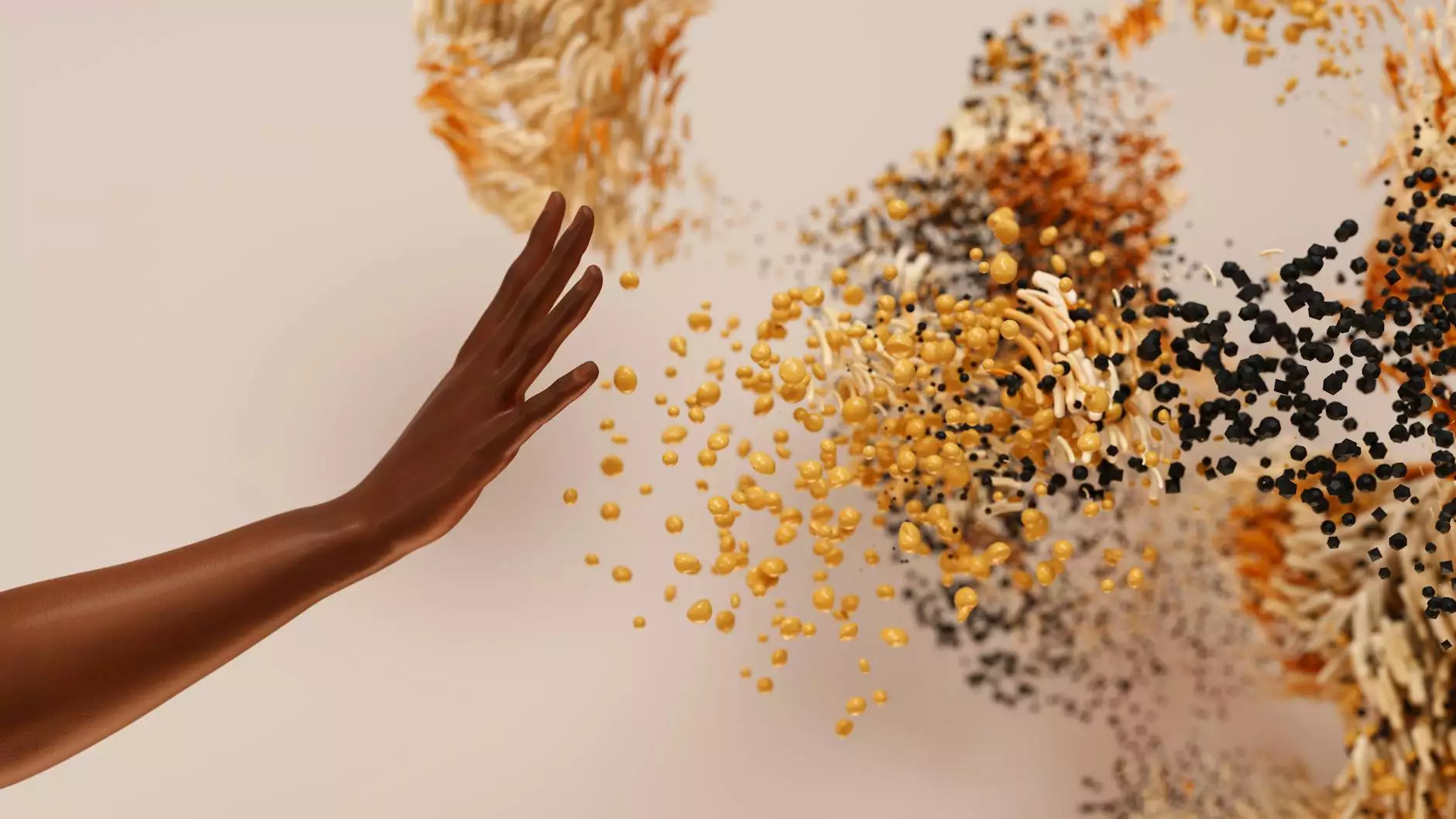
In the dynamic world of manufacturing, precision and efficiency are crucial for success. One of the leading methods that cater to these needs is CNC machining. This technology is revolutionizing the way metal fabricators operate, making it essential to understand its nuances, especially regarding CNC machining parts. This article delves into the intricacies of CNC machining parts, the processes involved, and how businesses like DeepMould.net are leveraging this technology to elevate their services.
What is CNC Machining?
CNC, or Computer Numerical Control, machining is a manufacturing process that utilizes programmable computer software to control the movement of production equipment. This technology allows for a higher degree of automation and precision compared to traditional machining methods. It encompasses various machining processes, including:
- Milling: The process of removing material from a workpiece using rotary cutters.
- Turning: A method where a cutting tool is moved in a linear fashion while the workpiece rotates.
- Drilling: Creating holes in a workpiece using a rotating drill bit.
- Wire EDM: A process that uses electrical discharges to cut through metal.
The Importance of CNC Machining Parts in Manufacturing
CNC machining parts are critical components that ensure the efficiency and accuracy of manufacturing processes. These parts are characterized by their high precision, allowing manufacturers to meet stringent specifications and standards. Here are some reasons why CNC machining parts are indispensable in the industry:
- Precision Engineering: CNC machining can achieve tolerances of up to ±0.001 inches, making it ideal for industries requiring exact specifications.
- Complex Geometries: The technology allows for the manufacturing of intricate shapes and designs that are difficult to achieve with manual techniques.
- Automation and Efficiency: Once programmed, CNC machines can operate autonomously, reducing the need for human intervention and increasing productivity.
- Cost-Effectiveness: Although the initial investment in CNC machinery can be high, the long-term savings realized through reduced labor costs and minimal material waste are significant.
Key Components of CNC Machining Parts
CNC machining parts consist of several key components that work together to achieve precise manufacturing results. Understanding these components can give businesses insights into how to optimize their operations:
The CNC Machine
The heart of the CNC machining process is the CNC machine itself. These machines come in various forms, including CNC mills, lathes, routers, and plasma cutters. Each machine serves a particular function, making it vital to choose the appropriate one based on the project requirements.
Workholding Devices
Workholding devices securely hold the workpiece in place during the machining process. These can include vises, clamps, or custom fixtures designed to stabilize parts that could be prone to movement. An effective workholding solution is critical for maintaining precision and accuracy.
Cutting Tools
CNC machining utilizes a variety of cutting tools that are selected based on the material type and the desired finish. Common cutting tools include:
- End Mills: Used for milling, these tools can create complex shapes and surfaces.
- Drills: Specifically designed for creating holes in materials.
- Insert Tools: Replaceable cutting inserts used in turning operations to enhance productivity.
Control Software
The software that drives CNC machines is equally important. It converts design files from CAD (Computer-Aided Design) into a format that the machine can interpret. This software enables the user to program complex cuts and movements.
Materials Used in CNC Machining Parts
Choosing the right material is fundamental to the quality and durability of CNC machining parts. Some commonly used materials include:
- Aluminum: Light, strong, and corrosion-resistant, aluminum is frequently used in aerospace and automotive applications.
- Steel: Known for its durability, steel is a versatile material used in various industries, particularly where strength is paramount.
- Titanium: Though more expensive, titanium offers unique properties like high strength-to-weight ratio and exceptional corrosion resistance.
- Plastics: Certain types of plastics are machined for use in applications where lightweight or insulation properties are desirable.
Applications of CNC Machining Parts
The versatility of CNC machining parts allows them to be used across various industries. Some notable applications include:
Aerospace Industry
CNC machining is essential in the aerospace industry, where precision and reliability are paramount. Components such as brackets, housings, and fasteners are frequently manufactured using CNC technology to ensure safety and performance.
Automotive Manufacturing
In the automotive sector, CNC machining parts are used to produce everything from engine components to transmission housings. The ability to produce lightweight yet durable parts is crucial for improving fuel efficiency.
Medical Devices
The medical field relies on CNC machining for the production of surgical instruments and implants. The high level of precision achieved by CNC machining ensures the production of high-quality medical devices that meet strict regulatory standards.
Advantages of CNC Machining for Metal Fabricators
For metal fabricators, embracing CNC technology offers numerous advantages that can significantly enhance their operations:
- Enhanced Precision: CNC machining minimizes human error, allowing for more accurate and repeatable manufacturing processes.
- Increased Production Speed: Automated processes lead to faster turnaround times for projects without sacrificing quality.
- Adaptability: CNC machines can be reprogrammed quickly for new projects, making them highly versatile in a fast-paced environment.
- Reduced Labor Costs: With automation, the need for extensive manual labor decreases, driving down overall production costs.
Challenges in CNC Machining Parts Production
While the benefits of CNC machining are significant, metal fabricators must also be aware of potential challenges:
- Initial Investment: The cost of CNC machinery and software can be substantial, potentially deterring smaller operations from investing in the technology.
- Skill Requirements: Operators need specialized training to effectively program and manage CNC machines, which can lead to a skills gap in the workforce.
- Maintenance: CNC machines require regular maintenance to ensure optimal performance, which may incur additional costs.
Choosing the Right CNC Machining Partner
As a metal fabricator, selecting the right CNC machining parts partner is critical for ensuring quality and efficiency in production. Consider the following factors when making your choice:
- Experience: Look for a partner with a proven track record in CNC machining and an extensive portfolio of projects similar to your needs.
- Technology: Ensure that they utilize modern CNC technology, including the latest machines and software.
- Quality Assurance: Investigate their processes for ensuring the quality of the finished parts, including inspection and testing protocols.
- Customer Support: Opt for a company that provides excellent customer service and communication throughout the project lifecycle.
Conclusion
The world of CNC machining parts is sophisticated and constantly evolving. For businesses in the metal fabrication sector, adopting CNC technology can lead to enhanced precision, increased efficiency, and significant cost savings over time. Companies like DeepMould.net are at the forefront of this evolution, providing clients with high-quality machining solutions that meet the demands of modern manufacturing.
As the industry continues to advance, staying informed about the latest technologies and trends in CNC machining will be essential for maintaining a competitive edge. Whether you are a seasoned metal fabricator or just starting, understanding the vital role of CNC machining parts can help you capitalize on new opportunities and drive your business forward.