Understanding Mould Tooling Design in China
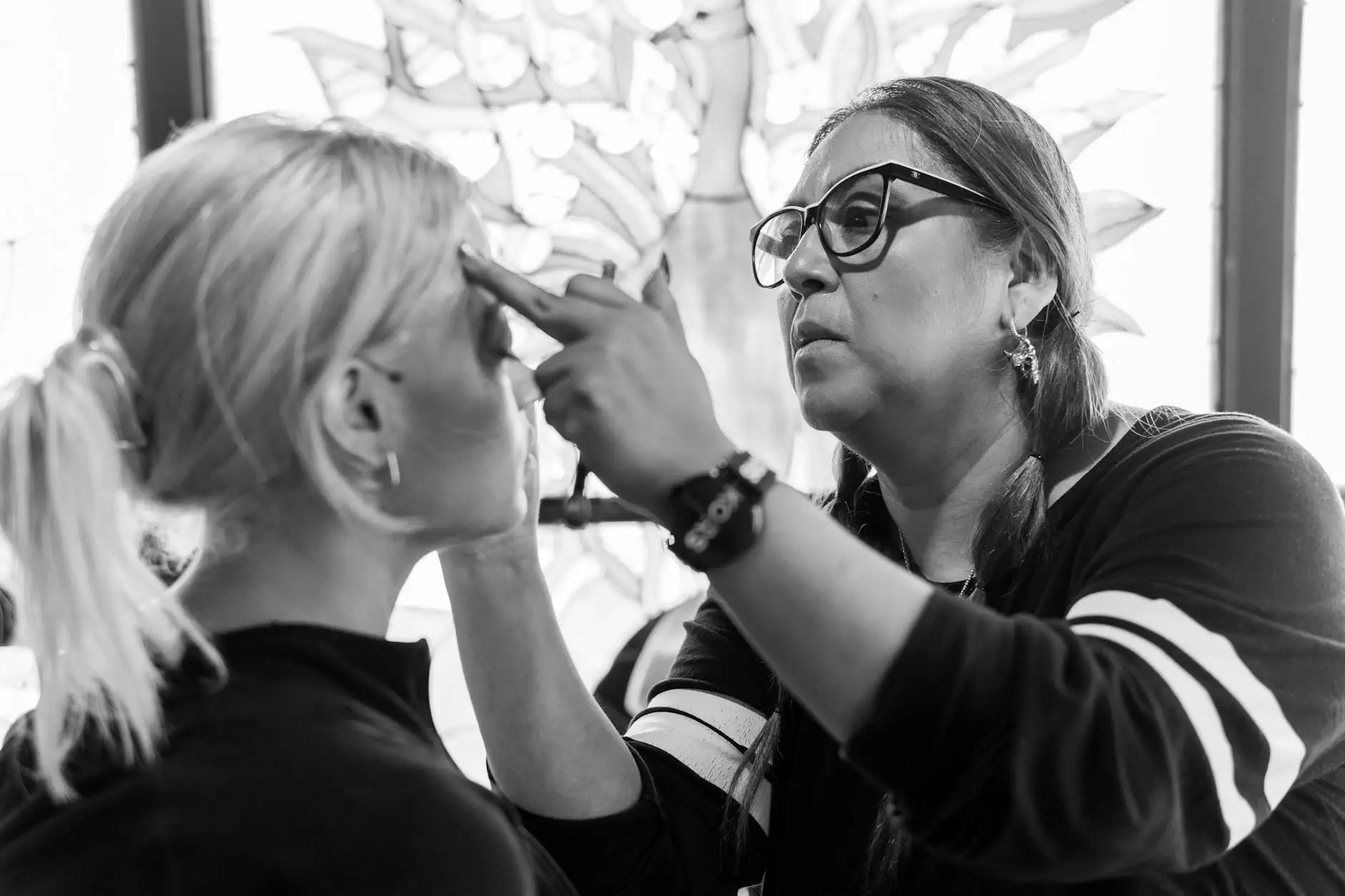
The realm of mould tooling design in China is a critical component in the manufacturing sector, encompassing various industries from automotive to consumer products. As a leading global manufacturing hub, China's advanced tooling techniques and skilled workforce play a pivotal role in shaping the future of product development. This article delves into the intricacies of mould tooling design, addressing its significance, the processes involved, and the strategic advantages of utilizing services from skilled fabricators such as deepmould.net.
The Significance of Mould Tooling Design
In any manufacturing operation, mould tooling design serves as the foundation for creating precision components. The significance of proper tooling design cannot be overstated. It impacts production efficiency, product quality, and overall cost-effectiveness.
- Cost Efficiency: Effective tooling design reduces wastage and rework, thereby lowering costs.
- Quality Assurance: Precision in tooling leads to superior product quality, ensuring that components meet the required specifications.
- Faster Time to Market: Streamlined tooling processes can significantly reduce lead times, allowing businesses to respond quickly to market demands.
- Innovation Enablement: Advanced tooling capabilities foster innovation, enabling manufacturers to explore new product designs and features.
Key Elements of Mould Tooling Design
When discussing mould tooling design in China, several critical elements come into play:
1. Material Selection
Choosing the right material for mould construction is essential. Common materials include:
- Steel: Durable and ideal for high-volume production.
- Aluminum: Lightweight and cost-effective for low-volume runs.
- Composite Materials: Often used for specific applications requiring unique properties.
2. Design Considerations
The design phase is crucial in mould tooling. Key considerations include:
- Complexity: The complexity of the design directly affects the tooling process.
- Tolerance Levels: High precision tolerances are necessary for parts that fit together accurately.
- Cooling Systems: Proper cooling design enhances cycle times and product quality.
3. Prototyping and Testing
Before full-scale production, prototyping and testing of moulds are conducted to ensure they meet design specifications. This phase includes:
- Vacuum Casting: Allows for the production of small batches to evaluate design and functionality.
- Simulation Software: Tools like CAD and CAE help visualize and optimize mould designs.
Process of Mould Tooling Design
The process of developing mould tooling design in China is meticulous, involving several stages:
1. Conceptualization
The process begins with the conceptualization of the mould. This involves brainstorming design ideas and assessing client requirements. Engaging with a skilled team can greatly influence the outcome.
2. Design and Engineering
Next, engineers utilize CAD software to design the mould. This phase is crucial as it translates concepts into executable designs. Iterative discussions with clients help refine the designs to meet all specifications.
3. Manufacturing
In the manufacturing phase, the actual mould is produced using techniques such as CNC machining, EDM, or injection moulding. The choice of processes depends on the design complexity and the material selected.
4. Quality Control
Quality assurance is paramount. Each mould undergoes rigorous testing to ensure it meets defined standards. This includes dimensional checks, functional tests, and surface inspections.
5. Delivery and Support
Once the mould passes inspection, it is delivered to the client. The support doesn’t end here; ongoing maintenance and modifications may be necessary as production requirements evolve.
Benefits of Choosing China for Mould Tooling Design
Opting for mould tooling design in China comes with several advantages:
1. Cost-Effectiveness
China offers competitive pricing without compromising on quality. The cost of skilled labor and material sourcing is generally lower than in many Western countries.
2. Advanced Technology
Chinese manufacturers continuously invest in modern technology and advanced machinery, facilitating cutting-edge tooling capabilities.
3. Skilled Workforce
The workforce in China is remarkably skilled and experienced, especially in areas like precision engineering and mould making. This expertise ensures high-quality outputs.
4. Quick Turnaround
With streamlined processes and abundant resources, companies can achieve shorter lead times, which is critical for industries facing tight deadlines.
Challenges in Mould Tooling Design
While there are significant advantages, it is important to acknowledge the challenges associated with mould tooling design in China:
1. Intellectual Property Concerns
Due to varying standards of IP protection, companies must carefully vet their partners and ensure proper agreements are in place to safeguard proprietary designs.
2. Quality Variability
Not all manufacturers adhere to the same quality standards. Conducting thorough due diligence before engaging with a supplier is essential.
3. Communication Barriers
Language and cultural differences can lead to miscommunications. Establishing clear communication protocols and having bilingual representatives can help mitigate this issue.
Conclusion
In conclusion, the field of mould tooling design in China stands as a testament to innovation and efficiency within the global manufacturing landscape. By understanding the significance, processes, and challenges involved, companies can make informed decisions when selecting a partner for their tooling needs. With businesses like deepmould.net specializing in metal fabrication, companies are equipped with the tools necessary for success. As the industry continues to evolve, staying abreast of trends and advancements will undoubtedly yield substantial benefits in competitive edge and product quality.
Frequently Asked Questions (FAQs)
1. What is mould tooling design?
Mould tooling design is the process of creating and optimizing the tools used to shape and manufacture products from various materials, often involving intricate specifications and tolerances.
2. Why is China a preferred location for mould tooling?
China is known for its cost-effective manufacturing, advanced technology, skilled labor, and quick turnaround times, making it an attractive location for mould tooling.
3. How can I ensure quality in tooling design?
Conduct thorough research on potential partners, request samples, and ensure proper quality control measures are in place. Engaging reputable suppliers like those at deepmould.net is recommended.
4. What materials are commonly used in mould making?
The most commonly used materials include steel, aluminum, and composite materials. The choice depends on the production volume and required characteristics.
5. What are some common applications of mould tooling?
Mould tooling is widely used in industries such as automotive, consumer electronics, packaging, and medical devices, facilitating the manufacture of components in these fields.
mould tooling design china