Understanding Shear Stress Units in Engineering Applications
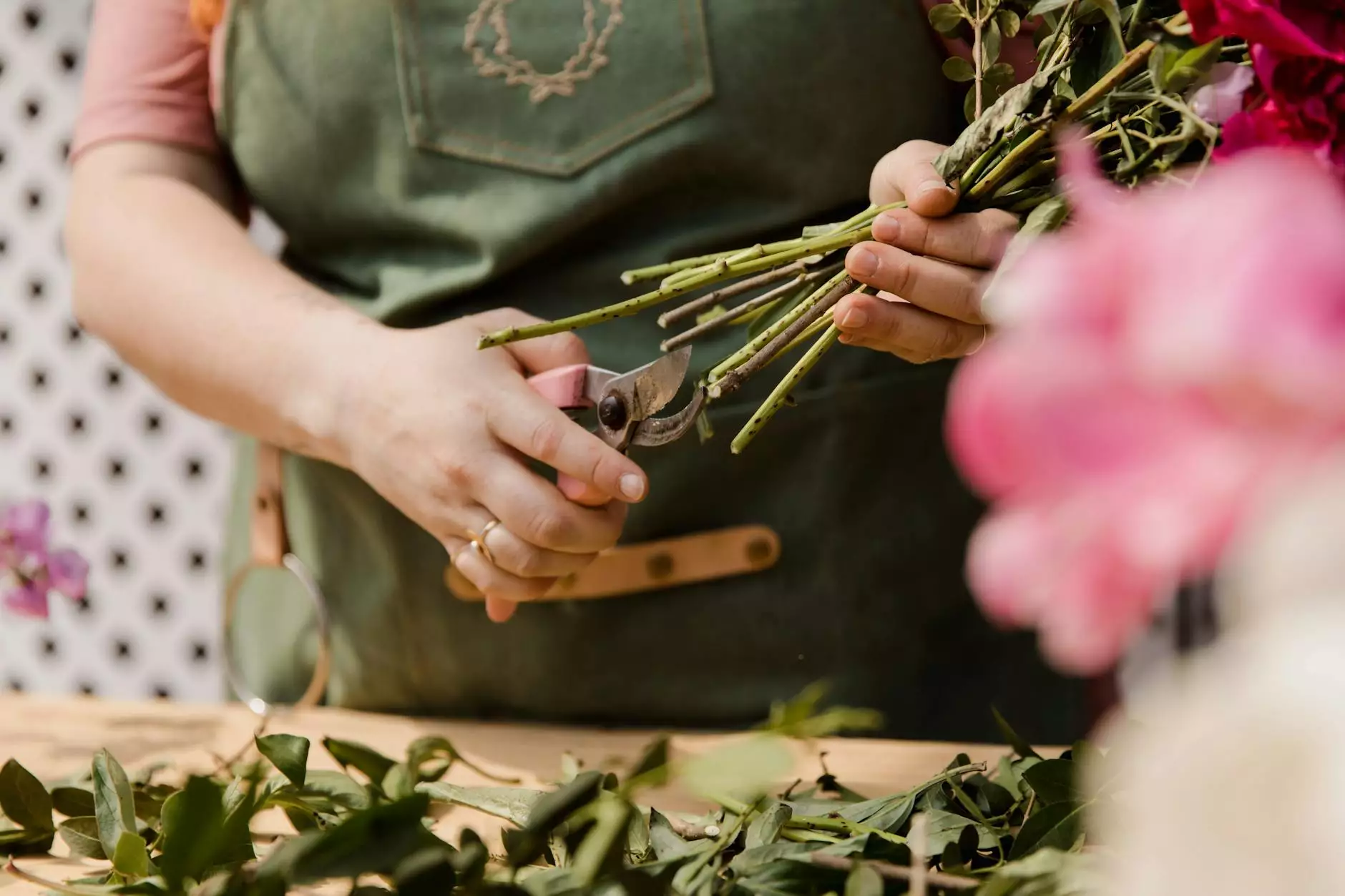
In the fields of engineering and material science, the concept of shear stress units is fundamental for analyzing the behavior of materials under diverse loading conditions. This article delves into the importance, calculation, and applications of shear stress units, particularly in the areas of auto repair, farm equipment repair, and structural engineering as showcased by Michael Smith Engineers.
What is Shear Stress?
Shear stress is defined as a measure of how much force is applied parallel to a material's surface area. In mathematical terms, shear stress (τ) can be expressed as:
τ = F / A
Where F is the force applied parallel to the surface, and A is the area over which the force is distributed. The resultant unit of shear stress is Newtons per square meter (N/m²), commonly termed as Pascals (Pa) in the International System of Units (SI).
Importance of Shear Stress Units
Understanding shear stress and its units is critical in various engineering applications. Here are a few reasons why:
- Material Selection: Engineers need to choose materials that can withstand specific shear stresses to ensure structural integrity.
- Failure Analysis: Many failures in engineering occur due to excessive shear stresses. Understanding this concept helps in predicting and preventing failures.
- Design Optimization: Knowledge of shear stress units aids in optimizing designs for better performance and efficiency.
Shear Stress in Auto Repair
In the auto repair industry, shear stress plays a pivotal role in the analysis of components such as gears, shafts, and fasteners. Auto mechanics must consider shear forces when repairing or replacing these components, as even the slightest miscalculation can lead to catastrophic failures.
Key Applications
Within the realm of auto repair, shear stress units are crucial for:
- Gear Systems: Gears operate by transferring torque and motion. Shear stress must be calculated to ensure that the gears can handle the operational loads.
- Bolted Joints: The integrity of a bolted joint is heavily dependent on the shear strength of the bolts. Proper calculations can help mechanics circumvent potential failures.
- Chassis and Suspension Components: These parts need careful analysis to ensure they can withstand shear loads from cornering and braking forces.
Shear Stress in Farm Equipment Repair
Similarly, the field of farm equipment repair necessitates a strong understanding of shear stress units. With equipment such as plows, harvesters, and tractors, shear forces can significantly impact performance and durability.
Significant Considerations
The following points illustrate the relevance of shear stress in farm equipment:
- Attachment Points: Implements that attach to tractors must be designed to handle shear forces during operation.
- Load Distribution: Farmers need to understand how shear stress affects load on equipment during use to avoid mechanical failures.
- Material Choices: Selecting the right materials that can withstand shear stress in farming equipment is critical for longevity.
Shear Stress in Structural Engineering
In structural engineering, shear stress has enormous implications. Engineers must design structures that effectively manage shear forces to maintain stability and safety.
Applications in Structural Engineering
Here are crucial aspects where shear stress units are applied in this discipline:
- Beams and Columns: The design of these critical components must incorporate shear stress calculations to ensure they perform under loads without failure.
- Structural Connections: Joints and connections must be analyzed for shear capacity to avoid potential structural collapse.
- Seismic Engineering: Buildings must be designed to withstand shear forces during earthquakes, which requires a deep understanding of shear stress applications.
Calculating Shear Stress
Knowing how to calculate shear stress is paramount for engineers and mechanics alike. The fundamental formula can be applied across various situations:
- Simple Calculation: For a rectangular area, if a force is applied, shear stress can be simply calculated using the formula mentioned earlier (τ = F / A).
- Vector Analysis: In complex loading conditions, vector analysis may be required to determine the resultant shear stress.
- Finite Element Analysis (FEA): For intricate structures, engineers often use FEA software to compute shear stress under multiple loading conditions.
Factors Affecting Shear Stress
Several factors can influence shear stress in a given component:
- Material Type: The inherent properties of materials, such as tensile strength and ductility, dictate how they respond to shear forces.
- Temperature: Changes in temperature can affect the mechanical properties of materials, thus influencing shear stress thresholds.
- Load Conditions: The manner and direction in which loads are applied can alter shear stress distributions within materials.
Shear Stress Testing Methods
To ensure that materials can withstand specific shear stresses, various testing methods are employed:
- Shear Tests: Standardized tests measure the shear strength of materials to validate their performance in real-world applications.
- Tensile Testing: Although primarily focused on tensile strength, these tests also provide insights into shear deformation characteristics.
- Dynamic Load Testing: This involves subjecting materials to varying loads and measuring their response to assess shear capacity.
Conclusion
In summary, the understanding of shear stress units is vital across multiple engineering domains, including auto repair, farm equipment repair, and structural engineering. It influences design decisions, failure analysis, and material selection, ensuring that structures and components maintain functionality and safety under various operational conditions. Professionals in these fields, such as those at Michael Smith Engineers, rely on a robust understanding of shear stress to deliver top-notch engineering solutions.
By adopting best practices concerning shear stress analysis and calculations, professionals can greatly enhance the effectiveness and reliability of their projects. Recognizing the intricate relationship between shear stress and material performance is essential for achieving engineering excellence.